Contact Information
Address: Gou Tang Town, Xinmi City, Henan Province
Telephone:0086-371-69251084
E-mail:zz@zz-zirconia.com
High-performance monoclinic zirconia
Fused calcia stabilized zirconia
Long-life fused calcia stabilized zirconia
Fused magnesia stabilized zirconia
Fused yttria stabilized zirconia / ytterbium stabilized zirconia
Zirconia based thermal spray powders (ZrO₂/Y₂O₃, ZrO₂/CaO,ZrO₂/MgO,Gd₂O₃/ZrO₂,ZrO₂/Y₂O₃-Yb₂O₃-Gd₂O₃)
Yttrium oxide thermal spray powders
Yttrium aluminum garnet thermal spray powders
Contact Phone:
Focus on us
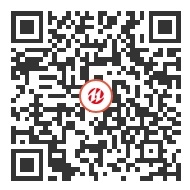
Online message
We will contact you within one working day. Please pay attention to your email.